Cast Your Vision:
Precision in Every Mold
Elevate your production with vacuum casting solutions. Our expertise ensures precision in every mold, delivering high-quality prototypes and end-use parts with exceptional detail and accuracy. From concept to creation, trust us to bring your vision to life with efficiency and reliability.
Vacuum Casting
Vacuum casting is a technique for creating high-quality prototypes or low-volume parts using inexpensive silicone molds. It is a replication method for making functional and end-use parts. Vacuum casting is the process of making plastic parts by using a vacuum to draw liquid material into a mold. Molds are usually made of silicone and are based on a 3D printed master model. Vacuum casting can produce high quality parts with complex shapes, fine details and low porosity. It is often used for prototyping and low volume production.
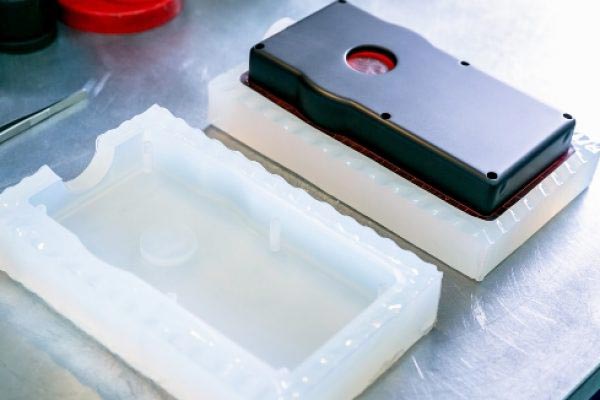
How Vacuum Casting Work
Vacuum casting is a streamlined and efficient process, encompassing several straightforward steps:
- Begin by crafting a 3D printed or CNC macnhined master model derived from a CAD file, serving as the template for the desired part.
- Construct a silicone mold by pouring liquid silicone over the master model, ensuring precise replication of its intricate details.
- Once the silicone has cured, carefully remove the master model from the mold, leaving behind a precise negative impression.
- Place the silicone mold in a vacuum chamber to prepare for the casting process, ensuring optimal conditions for material infiltration.
- Utilize vacuum pressure to fill the mold cavity with liquid material, allowing it to flow seamlessly into every nook and cranny of the mold.
- Apply heat and pressure to the mold to cure the liquid material, solidifying it into the desired shape.
- Finally, remove the cured part from the mold, unveiling a high-quality reproduction of the original master model.
This efficient process enables the rapid production of high-quality prototypes or low-volume parts with exceptional precision and detail, making vacuum casting a preferred choice for various manufacturing applications.
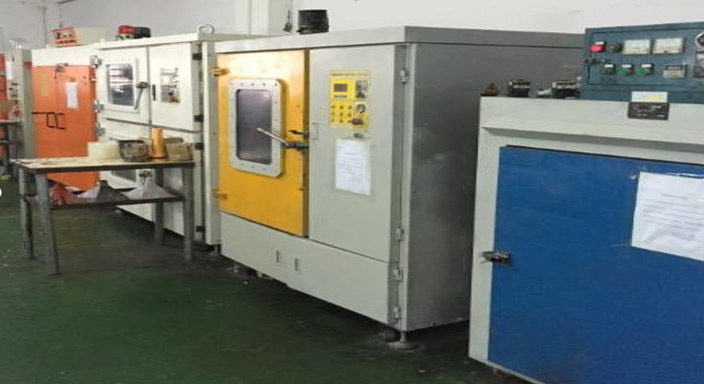
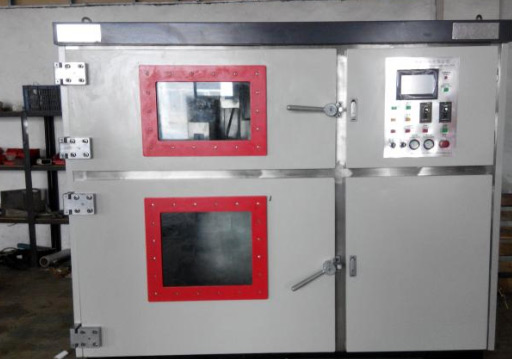
Advantages of Vacuum Casting
- Reduce the cost of mold making.
- Create precise and smooth parts.
- Parts have smooth textures and match the original closely.
- Design and build parts with versatility and complexity.
- A wide selection of materials such as plastic, rubber, composites and more.
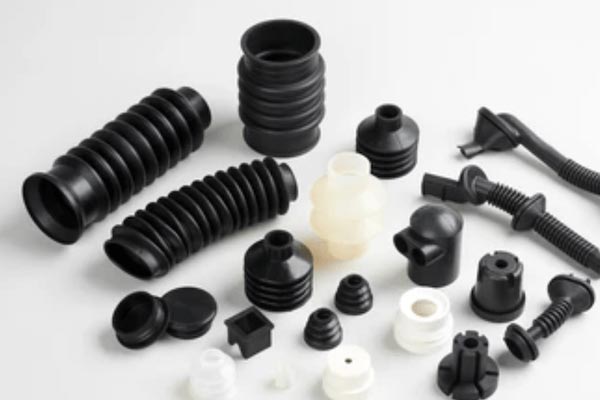
Vacuum Casting Materials and Applications
Vacuum casting materials are available in a wide range of choices. Including rubber, ABS, polycarbonate, and polypropylene.
Vacuum casting is used in a wide variety of industries such as automotive and aerospace, pharmaceutical and medical, telecommunications and engineering, food production and consumer goods.
The key characteristics of the materials used in the casting process are their durability and rapid formation. Vacuum casting is a key manufacturing process that has truly changed the manufacturing landscape for the better.
Talk To Us About Your Next Project
Beisi Rapid
Precision CNC machining allows designers, R&D teams, and manufacturers who rely on components supply to create complicated products without further machining.
Services
Contact Beisi
Address
Room 202, 2nd Floor, No. 53 Huanmao Road,
Xuecun, Torch Development Zone, Zhongshan City
Instant Call
+86 153 9880 0243